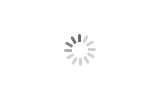
Hot Dross Recycle Machine
hot dross recycle machine is used for recycling aluminum from melting hot dross, recycle rate could be more than 85%
1. Recycle agent is de-slag flux.
2. Recycle rate: at least 85%
3. Treatment process: hot dross separate machine, dross cooling machine, dross milling and screening machine.
After collecting hot dross from melting furnace, continue to treat hot dross , recycle aluminum from hot dross, the full line including hot dross recycle machine, dross cooling machine, dross milling and screening machine.
hot dross recycle machine:
1. used for heating hot dross through de-slag flux, aluminum will become liquid, follow aluminum liquid channel for collecting, the remaining hot dross will go for cooling machine if dross capacity is not big, the remaining dross could be collected and sell to others.
2. more than 85% aluminum has been recycled throught hot dross recycle machine, the remaining dross go to cooling machine , cooling by water.
3. after cooling machine, the dross will be milled and screening into three different sizes of bag, small size is 40~80mesh, will be packed, middle size (1.5~3mm) could be used for reducing temperature agent during recycle aluminum liquid in hot dross recycle machine, big size(more than 3mm) could be melted again.
Two different designs for hot dross recycle machine:
1. with electric dross lifting machine,suitable for small capacity
2. without electric dross lifting machine, use forklift to loading dross, suitable for big capacity
Hot dross machine could be equiped with simple dust collecting machine:
Spare parts for hot dross recycle machine:
1. aluminum liquid pot
2. hot dross pot
3. mixing stir
The cold aluminum dross and hot aluminum dross treatment is same?
It is not same
1, for cold dross
if cold dross size is more than 100mm, need high speed milling machine to make it smaller,
then smaller cold dross go to rotary furnace ,cooling machine,milling and screening (capacity is not big), if capacity is big, then go to melting furnace for recycle.
if small cold dross, then go to melting furnace or rotary furnace for recycle
2.for hot dross
get hot dross from bottom of melting furnace, go to hot dross machine, to separate aluminum and dross, after recycle, the remaining dross connect with cooling machine and millling and screening machine.
So before as for quotation, please kindly let us know your dross type, dross size and monthly or daily dross production tons, if give space size , more better to send better suitable quotation.
How to improve the efficiency of the ash dross recycle and the separation effect of aluminum ash dross
How to improve the efficiency of the ash dross recycle machine and the separation effect of aluminum ash
To improve the efficiency of the ash stir fry machine and the separation effect of aluminum ash, the following aspects can be taken into consideration:
1、 Control the appropriate temperature
Temperature setting: The aluminum ash temperature in the ash roasting machine equipment should be controlled within a suitable range, generally recommended at around 800 degrees. Excessive temperature can damage equipment components (such as reamers), while insufficient temperature prevents effective separation of aluminum ash.
Temperature monitoring: Install temperature monitoring equipment to monitor temperature changes in real-time during the frying process, ensuring that the temperature remains stable within the optimal range.
2、 Optimize mixing operation
Stir evenly: During the frying process, ensure that the aluminum ash is evenly stirred in the frying machine. This helps to effectively separate aluminum ash from impurities and improve the separation efficiency.
Mixing time: Set the mixing time reasonably based on the characteristics and processing capacity of aluminum ash. Generally, stirring for ten to fifteen minutes can achieve a good separation effect.
3、 Ensure the normal operation of the equipment
Equipment maintenance: Regularly maintain and upkeep the ash roasting machine, check the wear and tear of each component of the equipment, replace damaged parts in a timely manner, and ensure that the equipment is in good operating condition.
Equipment upgrade: Consider upgrading the technology of the ash roasting machine by adopting more advanced separation technology and equipment to improve separation efficiency and effectiveness.
4、 Strengthen raw material management
Raw material quality: Ensuring the quality of aluminum ash raw materials, reducing impurity content, and helping to improve separation efficiency.
Raw material pretreatment: Pre treat aluminum ash, such as crushing, screening, etc., to improve its uniformity and processability.
5、 Improve operational skills
Training operators: Provide professional training to operators to enable them to proficiently master the operating skills and precautions of the ash roasting machine.
Standardized operation: Develop standardized operating procedures and job specifications to ensure that operators follow the standards and reduce the impact of human factors on separation effectiveness.
6、 Other measures
Environmental control: Keep the working environment of the ash roasting machine clean and ventilated, reduce the accumulation of dust and harmful gases, ensure the health of operators and the safe operation of equipment.
Recycling: Recycling and reusing separated aluminum and other valuable substances to improve resource utilization and economic benefits.