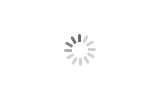
electrostatic powder spraying process
Brand CHANJEOU
Product origin FOSHAN
Delivery time 15 DAYS
Supply capacity 3000000 ton
Powder coating is a pure solid composition of the coating, can be fully automatic spraying, a large number of or ultra-sprayed powder, easy to be collected by the recovery system, to achieve the purpose of recycling. Therefore, the utilization rate of powder coatings can reach almost 100%, making the coating industry reduce the cost of waste treatment, while minimizing the degree of environmental pollution.
electrostatic powder coating
Use electrostatic powder spraying equipment (electrostatic spraying machine) to spray powder coating onto the surface of the workpiece. Under the action of static electricity, the powder will uniformly adsorb onto the surface of the workpiece, forming a powdery coating; The powder coating undergoes high-temperature baking, leveling, and solidification to become the final coating with different effects (different types of effects of powder coatings).
Detailed steps
1. Pre processing
Purpose: To remove oil stains, dust, and rust from the surface of the workpiece, and to generate a corrosion-resistant "phosphating layer" or "chroming layer" on the surface of the workpiece that can increase the adhesion of the spray coating. Main process steps: degreasing, rust removal, phosphating (chromizing), passivation. After pre-treatment, the workpiece not only has no oil, rust, or dust on the surface, but also forms a uniform and rough gray phosphating film (chrome film) on the originally silver white glossy surface, which is not easy to rust. It can prevent rust and increase the adhesion of the spray coating.
There are three common pre-treatment methods: soaking, spraying, and waterfall. Soaking requires multiple soaking tanks; Spraying requires setting up a spraying line on the spraying assembly line; The waterfall style is when the solution flows directly down the workpiece from a high place.
2. Electrostatic spraying
Purpose: To evenly spray powder coating onto the surface of the workpiece. Special workpieces (including areas prone to electrostatic shielding) should be sprayed using high-performance electrostatic spraying machines.
Process steps: Using the principle of electrostatic adsorption, evenly spray a layer of powder coating on the surface of the workpiece; The fallen powder is recovered through a recycling system.
3. Curing
Purpose: To solidify the sprayed powder onto the surface of the workpiece.
Process steps: Place the sprayed workpiece in a high-temperature furnace at around 200 ℃ for 20 minutes (the curing temperature and time depend on the selected powder quality, and the special low-temperature powder curing temperature is around 160 ℃, which saves more energy), so that the powder melts, flattens, and solidifies.